Jerico 4 Speed Revision 4.2 Transmission. The Revision 4.2 Includes all of the Benefits of the Revision 4 Plus: Ball Bearing Mid-Center Support (for increased strength and gear deflection) CNC Billet Shifting Forks CNC Billet Top Cover. Dog Rings and Sliders for Quick and Easy Shifting. Webbed Dog Rings. The primary four-speed manual transmissions used by Chevrolet are the Saginaw, Muncie and Borg Warner models, with Saginaw and Muncie units being specifically made for Chevrolet. Saginaw and Borg Warner models are normally used on general purpose applications.
Here is a guide to manual transmissions in Ford F-Series trucks Truck Years Type Description F-100 1956-1973 Borg Warner T-18 Top loaded heavy-duty 4-speed transmission with cast iron case and shift cover. Case casting number is 1301.
- Sep 10, 2020 Manual transmission problems can develop due to high mileage, abuse, or lack of proper maintenance. But they are rather rare. Most manual transmission issues originate not with the transmission itself, but from related components like the clutch assembly, linkage, or driveline: the components that transmit turning power from the transmission to the wheels.
- 1968- Ford Type E (aka Built or 2000e) 4-speed transmision Came in Anglia 105E, Cortina MkI, Lotus Cortina MkI, Cortina MkII to up to '68, Consul Classic, Consul Capri, Corsair, Escort TC, Mexico Mk1 and RS1600 MkI. 1976–1985 BC or BC4 1982–1995 BC5 1995-present IB5.
The following is a collection of information about the Chrysler 833 4-speed transmission. Thanks to all the contributors who helped with this Tech Article.
A Guide to Chrysler Four Speeds for Slant Six Engines by Doug Ahern
Chrysler began using '833' four speeds in passenger cars in 1964. The transmission was designed by Chrysler and manufactured by New Process Gear Co. Chrysler installed the 833 four speed behind the Slant Six at two different times. The first production four speed slant sixes were the 1964-66 A-body four speed cars. The second run of production four speed slant sixes began in 1975 with the release of the Overdrive A-833. From 1975 until 1987 the Overdrive four speed was installed in slant six applications of A-bodies, F-bodies, and light trucks (D100 & D200 series trucks). These applications were not ultra rare, but the slant six four speed production figures pale in comparison to the number of V8 cars that received A-833 four speeds. Since the A-833s installed behind slant sixes were basically the same transmissions installed in the V8 cars, a slant six owner looking to install an A-833 should be familiar with all the A-833s produced, including the ones used behind V8s.
How 833 Four Speeds Differ
There are several characteristics of the various A-833s that determine which four speeds fit in which chassis and with which engines. For the passenger cars, Chrysler manufactured two different length four speeds. The A/F-bodies received a short tailshaft A-833 and the B/C/E-bodies received a long tailshaft A-833. This difference is obvious when one of each type is sitting side by side, but either type is easily identified when it happens to be a stand alone unit. The short A/F-body tailshaft places the shifter pad behind the cross member mounting flange. (The 'shifter pad' is the 3 bolt bosses set in a triangle shaped pattern on the side of the tailshaft and servers as the mount point for the shifter). The 'cross member mount flange' is the 2 bolt pad on the bottom of the tailshaft that servers as a mount point for the cross member). A/F-body 4 speeds have only one shifter pad. The 1964-1969 B/C-body A-833s place the shifter pad ahead of the cross member mount flange, and the 1970-74 B/E-body 'long tail housing' four speed has two shifter pads, one ahead of the cross member mount flange (for B-bodies), and one behind the the cross member mount flange at the very end of the longer B/E tailshaft housing (this position is used in E-bodies).
The tail shaft length is the most apparent at first glance, but several of the smaller details can seriously hamstring a Saturday afternoon tranny swap. Perhaps the most troubling is the diameter of the Input Bearing Retainer (or IBR) that is located on the front of the four speed and fits into the large hole in the back of the bell housing. There were three different sizes on production four speeds. There was the 5.125' dia. IBR used on the 1975 and later Overdrive units, the 4.80' dia IBR used on 'Hemi' transmissions, and a 4.35' dia. IBR used on everything else. The 4.80' IBR 'Hemi' units are also known for their special 'course cut' gears, 18-spline input shaft (or 'Main Gear Drive' as it is referred to in parts manuals and FSMs), larger input bearing, and the requirement of a larger clutch release bearing. Calling it a 'Hemi' unit is not entirely correct, the 18 spline units were also used in most 440 applications as well. 'Hemi' units are rare compared to the regular 23 spline four speeds, however there are generally a few floating around at most major swap meets (bring your check book).
With any transmission swap, the drive shaft type must be carefully observed and adapted to the vehicle.
For the 'early' 1964-1965 A-833s, both the A-body and the B/C-body units used the ball & trunion output flange type. All later (66 & up) A-833s were slip yoke types. The 'ball & trunion' 4-speeds are easily identified by the four bolt non-sliding flange attached with a large nut on the end of the thicker cast iron tailshaft housing. The larger tail housing allows room for a third ball bearing at the rear of this 833, making it a very strong and stable gearbox. Even with this added bearing, this trans. should probably be avoided by anyone who doesn't have a 1965 or earlier car or isn't prepared for the challenge of shortening a ball & trunion drive shaft or locating the 'getting hard to find' B & T replacement parts.
Gear Ratios
There were at least six different gear sets used in production 833 four speeds. Below is a list of the most common gear sets:
(Year and Application 1st - 2nd - 3rd - 4th)
More on 833 ratios and applications (Click Here)
1964 thru midyear 1966 A-body 3.09:1 - 1.92:1 - 1.40:1 - 1:1 = G/RG and LA engines. (These all used a 4.35' IBR.)
1964 thru 1970 B/RB engine 2.66:1 - 1.91:1 - 1.39:1 - 1:1 = (The 'close ratio' V8 gearbox)
1970 T/A & AAR 340s 2.47:1 - 1.77:1 - 1.34:1 - 1:1, = 1970 thru 1974 high performance
(A 2.44 first gear was also produced in this time period and some units had 1.91:1 second gears.)
1975 thru 1987 Overdrive 3.09:1 - 1.67:1 - 1:1 - 0.73:1 (Trucks used a 0.71:1 fourth)
The Overdrive four speed was a regular A-833 with an overdriven gear set installed in place of the regular third gear. The shift lever on the side cover was flipped over to 'fool' the shifter into shifting from second to fourth and then back into third, which was the overdrive gear. The overdrive gear is very small and as a result, the mainshaft journal and splined hub is smaller. You can swap OD 833 parts as a set into the correct case for the mainshaft.
Strength Considerations
Chrysler engineers decided that Hemis required a beefier input shaft so the standard 23-spline shaft was replaced with a beefier 18-spline unit and a larger input bearing was used to accept the additional torque. Later Chrysler decided that the high performance 440s needed this beefiness as well. It is one of a few aspects that set the 'Hemi' four speeds apart from the standard 4.35' A-833s as being extra beefy. As far as strength is concerned, outside of the input shaft, the input bearing, the retainer and some special gear sets, there were no additional measures added to A-833s for Hemis. In the Sixties the only other difference between a Hemi A-833 and a Slant Six A-833 were the gear ratios used. The Slant Six 4-speed is just as beefy as the Street 'Max Wedge' V-8 units.
The Overdrive 833s used a giant 5.125' IBR and the super large input bearing behind the IBR as sort of a reinforcement measure. Most manual transmissions spend most of their time in a 1 to 1 ratio top gear. When a non-Overdrive A-833 is in top gear (fourth), the input shaft is locked to the output shaft by a sliding collar. This locks the two shafts together creating a 1:1 output ratio, hence the term 'direct drive'. In fourth gear, the countershaft (cluster gear) in these transmissions is along for the ride and spins with no power load being applied. In an Overdrive four speed, since third gear is really the 'direct drive' gear, and top gear is really 'third gear', the transmission spends most of its time with torque being applied through the countershaft and back up to the output shaft, just like the lower 'gear reduction' ratios. The Chrysler engineered solution for the added strain on the input bearing was to increase its diameter and the diameter of the IBR (hence the use of #308 type front bearing). Because of the final drive speed difference between the front input shaft and the main output shaft while the OD 833 is in long term highway cruising mode, the roller bearings between the two shafts do more work, and as a result, show more wear. It is important to inspect these rollers and the mating shaft surfaces (races) for pitting whenever rebuilding an OD 833.
Bell housings
Slant Six owners have two bell housing options to mate G/RG blocks to 833s. The original 1964-66 Slant Six four speed bell housing is a great candidate and accepts any A-833 with a 4.35' IBR profile. These units were all cast iron. While these bell housings are becoming increasingly hard to come by, the inspection plate, dust shield, clutch fork, and fork boot can all be swapped-over from a Sixties G/RG with an A-903 three speed. The casting numbers for the early cast iron bell housings are 2463025, 2463027, and 2468431.
Mopar 3-speed Info. (Click Here)
A much cheaper and plentiful bell housing to use is the 1975-81 A-833 Overdrive Slant Six bell housing. The upshot of this bell housing is that it is cast aluminum, the downside is that it only accepts A-833s with 5.125' IBR profiles. When looking for donor vehicles in salvage yards, don't' walk past late seventies slant six three speed cars. Chrysler used the same bell housing for both A-833 Overdrives and three speeds by placing both bolt patterns on the same bell housing. A casting number for this bell housing is 3743645. (This is a 1975 number, no doubt later bell housings used other numbers.) The Overdrive bell housings use a unique clutch fork mount that you will not find on regular three speed or four speed bell housings. Make sure you keep track of the correct fork and its mounting stand that bolts inside of the bell housing!
The Overdrive bell housings can be modified to accept either the 4.80' or the 4.35' IBR. A ring must be fitted to the bell housing to reduce its IBR hole from 5.125' to 4.35' or 4.80'. This ring must maintain the hole's exact center! A skilled and caring machinist should be able to accomplish this without issue. Good planning would provide the machinist with the bell housing and IBR you plan to use so a perfect fit can be achieved.
Once upon a time Chrysler made IBRs that fit the standard 23-spline case and mated to the 4.80' and 5.125' bell housings, however these appear to have been discontinued and snatched up a while ago. An additional option for someone trying to put a close ratio 4.35' IBR A-833 behind an Overdrive bell housing is to use an Overdrive front case and IBR and replace all the internal parts with those from a closer ratio four speed. This swap requires changing all gear sets, shafts and the countershaft.
Shifters, Shift Rods, and Floor Humps
All Chrysler A-833s were equipped with Hurst shifters with the exception of the Inland shifter debacle of 1966-1968. The Inlands are pretty recognizable (they don't look like Hurst shifters!) and I believe the Inland-Chrysler relationship was rekindled in the Seventies with the Chrysler floor shift A-body and E-body three speeds. A nice feature of an Inland shifter is that it has a pull-up reverse lockout lever. Enough talk about Inland, the Hurst units are the ones to have! There was a huge variety of OEM Hurst shifters built and Hurst is still happy to fix you up with anything you need from shift rods to new shifters.
It is important to point out that there is a shifter mounting plate or 'adapter' which goes between the transmission's 3 bolt shifter mount and the 2 hole shifter 'box'. There are many different adapter plates used for different chassis. The shifter adapter plate will angle the shifter lever and has an effect on shift rod lengths. There are many variations over the years and needless to say, you need the right ones for your setup. Shifter linkage rod length changed between the different platforms (A, B/C, and E bodies) as the adapter plate / shifter was placed at different locations along the tailshaft. Additionally, the A-body Overdrive A-833s used a different 3rd-4th rod to accommodate the up-side-down shift operating lever. On top of all that, the hole in the lever that the linkage rods fit into changed in diameter at some point during the four speed shifter years.
(Needless to say that it is best to get your shifter as a complete set of parts and from the same year chassis you are working with.)
Four speed cars require a special floorboard hump alongside the trans tunnel to clear the shift rods and the shifter. This is because the floor shift linkage runs over the top of the torsion bar / trans mount cross member, basically through an area which is currently part of the passenger compartment of an automatic car. From the factory, these floor humps were stamped steel pieces that were welded to the regular floorboard after an appropriately sized hole (read: big) was cut out of a common floor pan. Any automatic to four speed conversion will require cutting a hole and adding a hump extension. The hump's size and shape varied from platform to platform as well as year to year in some cases. Depending on the year and platform of the car, you will either have to procure an original hump cut from a donor car or find a fiberglass or steel reproduction. Of course, if you are handy with sheet metal, you can fabricate your own. For the A-bodies, the OEM stampings changed at least four times as follows:
1964-65 round hole for shifter.
1966 hump is the same as 1964-65, except an oblong shifter hole is used. 1967-74 available as a fiberglass reproduction, as well as a new stamped steel piece.
1975-76 similar to the 1967-74 floor humps. These turn up on eBay almost weekly. Brewers also sells new and used pieces. At one time they were producing the hump for the early A-body but I believe that piece is discontinued.
Flywheels, Clutches, and Clutch Linkage
For bell housing clearance reasons, the small 124 tooth flywheel must be used on both the 1964-66 bell housing and the 1975-81 Overdrive A-833 bell housing. Larger 130 tooth and 143 tooth flywheels do not fit these bell housings (the starter will not engage ring teeth). When locating a flywheel, be sure that the center hole matches your crank's register hub. A 1963-67 flywheel must be used with a 1963-67 crank and a later flywheel must be used with a later crank. (Measure your crankshaft hub.)
While the 124 tooth flywheel is very common (used on all passenger car slant six manual transmission applications) and generally dirt cheap, its size limits clutch options significantly. Over the counter clutch options include the original Borg and Beck 9-1/8' and 9-1/4' clutches. Over the years the pressure plates for these clutches were manufactured with various spring weights. A clutch repair shop that services pressure plates can rebuild a pressure plate with additional springs for more 'holding power' if you are building a high power slant six. Link to www.slantsix.org clutch overview (Click Here)
There is a heavy duty 10' truck clutch that does fit, however special attention needs to be paid to the clutch linkage as the heavy weight of the clutch's springs can cause failure in the stock clutch linkage system. (More information on this is currently being gathered.) A Georgia Slant Six aficionado, David Elder, installed one of these clutches in his 1964 Valiant. The additional force of the clutch action ripped a hole in the inside fender apron where the clutch linkage z-bar pivot mounts to the chassis. Reinforcement of the z-bar and its mounting points are in order anytime the clutch pressure plate spring force is increased. Bracing the clutch pedal / brake via the Master Cylinder bolts would also be a good measure as would gusseting an original thirty year old z-bar arm.
As far as clutch linkage is concerned, stock slant six clutch linkage for three speed cars can be used. On the original 1964-66 A-833 cars, everything between the driver's left foot and the clutch release bearing (AKA the throw out bearing) is the exact same setup as the 1963-1966 slant six A-903 three speed cars. This includes the z-bar (torque shaft), clutch fork and push rod. On later A-bodies and other platforms, you may need to 'mix and match' linkage parts. Be aware that the early bell housing used the small slant six clutch fork and the slant six z-bar needs to be used with it to get the correct movement on the release bearing. The later Overdrive bell housings used the longer V8 clutch fork.
Truck Overdrive four speeds: Don't get sidetracked!
There were two types of four speeds installed in trucks in the late seventies and early eighties. One was the A-833 overdrive four speed which is basically a passenger car 833 four speed and shifts like one. The other four speed was the A-435 which is a huge truck four speed that shifts like a truck, it has a truck non-syncronized 'granny low' first gear. The A-435 requires a huge cast iron bell housing and a 143 tooth flywheel. The combo of the bell housing and the A-435 wouldn't fit in an A-body unless you hacked the firewall and the trans tunnel to pieces, and of course the shift knob of a A-435 would probably bang into the rear view mirror on an A-body! Once you are familiar with identifying A-833s, there is no way you'd confuse the two transmissions (the A-435 is a top loader), however it is good to know that there were multiple four speed types installed in the trucks to hopefully prevent a drive halfway across the state to a junkyard that has the wrong truck four speed (call ahead and ask questions!).
Recommended Reading
Any 1964 and later Factory Service Manual (FSM) will discuss maintenance and repairs that are required of four speed gear boxes. For proper clutch installation, shifter adjustment, and torque specs, there is no substitute for an FSM. Several Mopar magazines have run various four speed articles over the years. The most informative by far have been the articles written by Richard Ehrenberg, 'A Need Four-Speed' rebuild and beef up of the A-833 gearbox, published in Mopar Action (August 1993) and again in the Mopar Action Tech Special #3 (1995). This article discusses the A-833s in depth. For additional information on swapping four speeds into various platform cars, you should locate the December 1996 Mopar Action which contains a segment of their 'Engine Swap Series' that is devoted to four speeds. There were several smaller articles in Mopar Action, Mopar Muscle, and High Performance Mopar that covered shifters and drive shafts that are relevant as well.
Final Notes
Thanks to Richard Ehrenberg for writing the great articles about four speeds that have been published several times over in Mopar Action. Special thanks are due to Bill Elder for showing me how everything inside an A-833 works, and to his son David Elder for always being just as happy to talk about four speeds as I am.
Doug Ahern - Athens, GA
More info about Mopar Manual Transmissions at: http://www.autohobbydigest.com/ablues-2.html
Internet Q & A, In Response To: 4 speed trans swap into '66 Valiant wagon (Gary L)
Q: I just found a 4 speed from a 1977 Dodge D100 short bed half-ton pickup, with a /6, at a local salvage yard. Will it swap into my 1966 Valiant wagon, which currently has a 225 /6 from a 75 Aspen? What other parts should I grab from the donor truck ( i.e. shift linkage, bell housing, clutch, etc.)? Will I need to change the cross member that holds up the trans? Are there any modifications that I need to do (i.e. shorten the drive shaft)? Will a floor hump from a Duster, which had a 3 speed on the floor, work? What parts do I need to buy new when I do the swap (i.e. clutch, throw-out bearing, etc.)? Any tips would be appreciated.
A: There were two type of 4 speeds installed in trucks in those years. One is the A-833 overdrive 4 speed which is basically a passenger car 4 speed and shifts like one. The other 4 speed is the A435 which is a huge truck 4 speed that shifts like a truck with a truck 'granny low'. The 435 requires a huge cast iron bell housing (BH) and a 143 tooth flywheel. The combo of the BH and the 435 wouldn't fit in an A-body unless you hacked the firewall and the trans tunnel to pieces. For quick identification: the 435's shifter is integrated into the top of the trans. with external shift rods (linkage). On the 833 OD, the shifter is side hung on the tailshaft and has external shift rods - linkage running up to the side cover. (The 833 trans is a 'side loader')
If the donor vehicle (truck) has an 833 4 speed, it's a long tailshaft 833 unit and it won't really directly bolt into an A-body. It could be made to fit, but it would require some significant modifications. A long tailshaft 4 speed in an A-body will place the front B-Body location shifter directly in the path of the upper trans. torsion bar cross member section that goes up and over the trans and joins the the two t-bar mounting frame rails. You'd have to cut the cross member and either try to build a second one behind or ahead of the old one, or drive without one (not advised at all!). Another option is available if the long truck tail housing has the 'dual location' shifter mounting pads use for the B & E Body. If so equipped, you can make up a plate that spans across the two shifter mount positions and then mount your shifter along that 'adapter plate'. Below is more detail on that swap, it has been done. It might still be worth while to grab the long tailshaft OD 4-speed if the price is right and then sell or trade it to raise funds for the proper A/F body unit. The A/F OD 833 is much more common than the B/E/truck 4 speed.
Adapting a Long Tail housing B/E Body Trans to the A-Body by Dave Clement
When I swapped from the 3 speed column shift in my 68 Barracuda to the long tailshaft 833 OD 4-speed from a D100 truck, the only fabricating I had to do (besides the tunnel extension) was to make a mounting plate that positioned the shifter forward from the rear shifter mount and shorten the drive shaft. Here are the things I found out about this conversion:
1. The three speed bell housing in my 68 Barracuda did not have the correct bolt pattern for the 4-speed and the bearing support pilot hole was to small. I used the bell housing from the pickup.
2. The 3 speed's rear tranny mount transferred directly to the OD 4 speed and mounted up with no modifications to the cross member. The distance from the face of the tranny to the center line of the tranny mount was the same for both the 3 speed and 4 speed and the distance down from the centerline of the output shaft to the face of the tranny mount were the same. I read that early B-bodies did have tranny mounts in a different location. Later, all trannies used the tranny mounts in the same position.
3. The z-bar pivot on the 3 speed bell housing transferred directly to the 4 speed bell housing. The truck pivot was longer and in a different position but its mounting pad is in the same location.
4. I had to use the truck clutch fork because its pivot in the bell housing was a ball on the truck and a bracket in the 3 speed and they were not interchangeable (bracket bolts on with two screws; the ball pivot is a single thread-in post). The extra 1' length on the truck clutch fork does not interfere or cause any problems. I am running 6 into 2 headers with this setup.
5. The front boss on the front shifter pad on the OD 4 speed interferes with the A-body torsion bar cross member. You can either dent the cross member or do as I did and cut the boss off the trans. tail housing.
6. The output shaft on the 3 speed is smaller than the 4 speed. You will need a slip yoke from either a 4 speed or 727 car with a universal joint size that matches your drive shaft (or get a crossover 'problem solver' universal joint).
7. I forget the actual dimension but I had to shorten the drive shaft about 3 3/8'. (Measure everything once the setup is in the vehicle and resting on the ground at ride height.)
8. I used standard 4 speed A-Body shifter rods. The flipped over 3/4 lever puts the rod close to the cross member but since I was fabricating a mounting plate anyway I made sure that I had enough clearance before drilling the shifter mounting holes in the new plate. I used the standard A-Body shift mounting plate (adapter) along with about 1/2' of spacers on my fabricated mounting plate to locate the shifter towards the left so it came through the floor in the correct position, closer to the driver.
9. The shifter mechanism that was on the truck was made by Hurst and looked just like a Competition Plus shifter without the adjustable stops and had the bayonet attachment for the shifter handle. I used this shifter with a handle off an old 3 speed shifter. I did have to ream out one hole on the shifter and one of the tranny levers to get the A-Body linkage rods to fit.
10. The speedo drive mechanism and gear from the 3 speed swapped directly into the OD 4 speed so calibrating the speedo for the tire diameter was not an issue.
Dave Clement
Conversion info on installing an 833 4-Speed on a 66 A-Body
Muncie 4 Speed Manual Transmission
Let's say you find an A/F Body OD 833 to install in your early A-Body. Here is the lowdown on how to install it into a 66 A-Body: Your 66 drive shaft will work as long as you have the proper slip yoke for the trans. (The slid-in yoke started in 66, earlier cars with the ball & trunion setup need the earlier trans or a different drive shaft and speedo drive setup.) You'll need a 75-80 6 3 speed/4 speed bell housing (BH), dust shield and inspection plate along with the matching clutch fork. (Note the OD BH clutch fork is the long one that was also used on LA V8s. and not the smaller 6 fork used on sixties G/RG 3 speeds and 4 speeds.) You'll also need the right flywheel to mate to your SL6 crank. If nothing else I can tell you that your 75 crank will not work with a 67 or earlier flywheel (center register is smaller). The A/F body G/RG BH requires a smaller 124 tooth flywheel that was used on all passenger car 6 3 speeds and 4 speeds. The truck 'granny low' BH used a larger 143 tooth flywheel.
If you are currently running an automatic, you need a 63-66 A-body clutch pedal setup, your crankshaft needs a pilot bushing, and you need to cut a big hole in the floor to accommodate the 4 speed shifter and shift rods. Of course, you'll need to cover this hole. The 4 speed hump to use is the 64-66 4 speed A-body hump which can be somewhat elusive, but not impossible to find. (There was one at Carlisle last week for $85, Brewers used to produce fiberglass repros, and I've seen 3 factory humps in junkyards in the last 3-4 years.) It doesn't have to be an original hump, you can fabricate a suitable cover out of sheet metal. You will also need a 63-66 3 speed/4 speed z-bar (torque shaft) and mounting brackets. By the way, if you had gone to Carlisle (or other big Mopar swap meets) with the idea of collecting all the required parts to 'OD-4spd-ize' an A-body, you could have done it for anywhere from $200 to $500 for everything. You just need to know what you are looking for and as always, hope that the trans itself is in good working condition. (If the trans. needs rebuilding, see below.)
Rebuilding the Chrysler New Process 833 4-Speeds by Rob Armstrong (Dusteridiot)
Here are some of the assembly instructions for the 1975-1987 A-833 OD transmission.
Assembly items needed are similar to the regular A-833 with a couple of exceptions. If the countershaft gear cluster is too large to put into place, then wiggle the mainshaft assembly in around it. The drive pinion gear is too large to insert properly with the countershaft gear cluster in place. The drive pinion bearing is a #308, yet the main shaft rear drive bearing is a #307. It is good to have a friend help out so you can pay attention to details while they do some of the lifting and placing work.
Special tip: On an OD 833, never slide the front synchro clutch sleeve (shift fork collar) 'rearward' to engage the OD synchro and gear. The OD gear is so small that it will not stop the sleeve's travel so it will overextend and allow the spring loaded clutch struts to pop out of position. (These struts can be reinserted but it is a lot of extra work, especially on an assembled tranny.
With the mainshaft parts all assembled, tail extension housing installed and the reverse gear idler removed from the case:
1) Assemble countershaft cluster gear bearing set (needle bearings and washers) using heavy grease to hold them in place. Cut off a broom handle or rod stock of similar diameter to the countershaft itself but 1/4' less than the length and insert this 'dummy shaft' into the cluster gear, in place of the countershaft. This will keep your needle bearings and washers in place during the assembly process.
2) Insert the countershaft thrust washers into keyed case slots and stick them down with a glob of sticky grease.
3) Insert the countershaft gear cluster from the rear and leave it loose in the bottom of the case. Keep it stable with one hand if you move the case around or change the case's orientation.
4) Make sure the input shaft needle bearings are seated and “stuck down” with grease to the inside of the Drive Pinion gear. Double check their proper placement. With the #308 bearing installed, insert the drive pinion through the front of the case until seated. You can then install the drive pinion retainer with its seal and gasket (sometimes called the pilot retainer or input bearing retainer).
A 1” hole will need to be drilled into your bench for the next step. A custom stand with a piece of 1 ¼” pipe standing up to hold the tranny nose down will also work.
5) Tip case on its face, inserting the input shaft/bearing retainer into the hole. (This is where a friend’s help is needed.) Have your friend insert the mainshaft/tailshaft assembly into the butt of the tranny case (don't forget the tail housing gasket), while you guide the assembly, making sure you don’t lose your struts/shift rings/synchros. Rest the nose of the mainshaft on the outer edge of the drive pinion for a 'rest stop'. Now make sure you haven’t lost any of the shift rings and struts. Also make sure your 3rd gear (front) synchro is in place. Now move the mainshaft assembly to install it into the roller bearings of the drive pinion. It should drop in and mate together with little resistance.
6) Twist the tailshaft housing until it clears the countershaft hole, then insert one bolt to hold it in place.
7) Line up the countershaft gear “cluster” with the holes in the case (make sure your thrust washers are still in place and aligned properly with the case holes). Your piece of broomstick will start to come out if aligned correctly. Grease up the countershaft and drive it in from the backside. The broomstick will fall out the bottom, leaving the needle bearings in position and the countershaft installed (make sure to line up the small woodruff key in the shaft and case before driving it home the last ½”).
9) Put tranny on its belly. Remove tailshaft housing bolt. Twist the housing 30 degrees the other direction to clear reverse idler gear/selector shaft hole, and insert your “keeper” bolt again in the most available hole.
10) Insert reverse lever shaft and fork and gear. Have your helper hold the idler assembly while you drive the greased shaft and woodruff key set in. Install the reverse shift light switch and the reverse detent assembly (the plug with the spring and ball bearing).
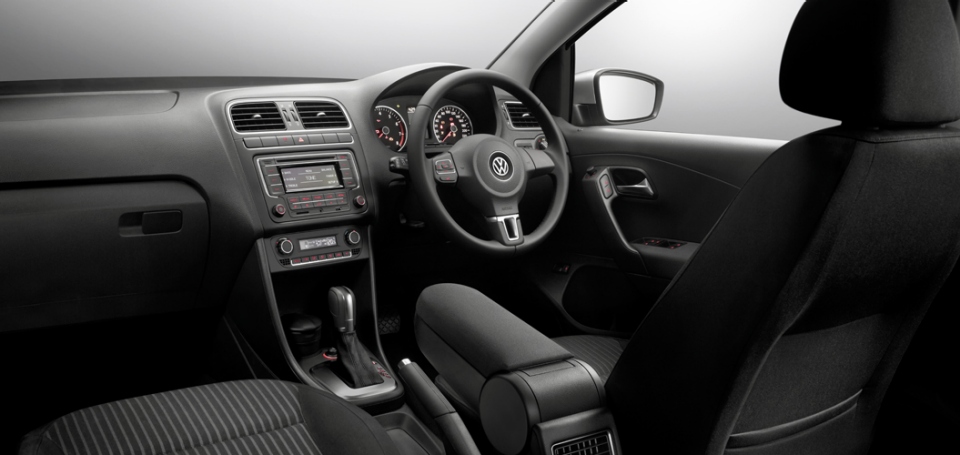
11) Grease the tailshaft seal, rotate tail housing and gasket into proper alignment. Insert the remaining bolts and torque to specs.
12) Replace the o-ring seals on shift levers in side cover/plate. Check for the special shoulder screws and note the proper holes they go in. (One may extend through the cover plate and into a counter bored hole in the case, mark that bolt and hole).
13) Install shift forks into the case onto the shift ring's grooves with some heavy grease. Place the side cover gasket over the access hole. Have a friend hold the shift forks in place while you install the side cover. You will have to use a screwdriver to push on the cover levers and shove the “spindles” into their detents before the side cover will set completely into place. Bolt the plate into place then bolt the shift levers into place.
14) Install all the plugs including the countershaft’s front expansion plug. (Get a new one, Dorman brand) or repair you old plug using epoxy, solder or RTV) Install the shifter adapter plate on tailshaft housing.
Congrats! You have a rebuilt a New Process 833 OD 4-speed tranny. Reinstall it into your car and fill with the oil of choice. (90 weight oil,motor oil or ATF all work well) Don’t forget how those shift rods were installed with the 3rd - 4th lever flipped upside-down. It is a good idea to take a photo or mark the rods with different color paint to help keep track of where and how they go in.
Non-OD Assembly Instructions
4 Speed Manual Transmission For Sale
Great OD 4-speed assembly review by Rob Armstrong. The earlier 1 to 1 final drive 4-speeds can be assembled a little differently then the OD unit. On the early “3.09 first gear' 833, the input shaft (drive shaft) has to be installed from the inside of the case. Let's run through the assembly as it applies to the early “non-overdrive” 833 4-speed box. As already noted, this assembly process works best when the gearbox is standing on end. I have a 1 inch hole drilled through my work bench because you *need* the tranny standing up on its 'face' with the input shaft through the hole and its rear main case to tail housing opening in the air. Position the side cover opening so you can look inside the case easily.
Before starting any assembly work, take a good look at the end of that main shaft. You should find a nice big smooth 45º chamfer (angle) at the tip. Some of these machined angles can be rough or small so I recommend that you grind or file on this edge / area a little so it is more of a smooth radius. Doing this prevents 'knocking-down' the needle bearings, nested in the input shaft, as the mainshaft slips in.
On the 1 ti 1 trannies, you can install the mainshaft assy.. with the counter shaft and reverse gear already installed in the case. To do this, the reverse 'idler gear' must be centered on the middle of its small shaft. You also need to 'hang' the 3-4th clutch sleeve (sliding collar) right at the end of it's travel, at the end of the mainshaft assy. This is tricky, I put some real sticky silicon grease on it to *try* to keep it from falling off when the whole assy is hanging upside-down, on the way into the case. Don't get too 'pissed' if the collar falls off and the 3 toggles (struts) fly around (they are under spring load).
Dodge 4 Speed Manual Transmission
OK, 'Indexing' is a key point, but where, what, how?? On the sliding collar, put a paint mark to show where the toggles (struts) are located. If you look close, you may find a factory paint mark already there. You need to know where these toggles are because you can not see them with the collar pulled forward. Also mark the front synchro ring, out at its teeth, showing where its block / notches are (where the toggles fit in). Basically you need to know where these locations are because the collar blocks your view when it is pulled forward. (And yes, the more forward the collar is, the easier the tranny will go together.
Now the fun starts. Get another person to help during this next step. It is a '4 hand job'.
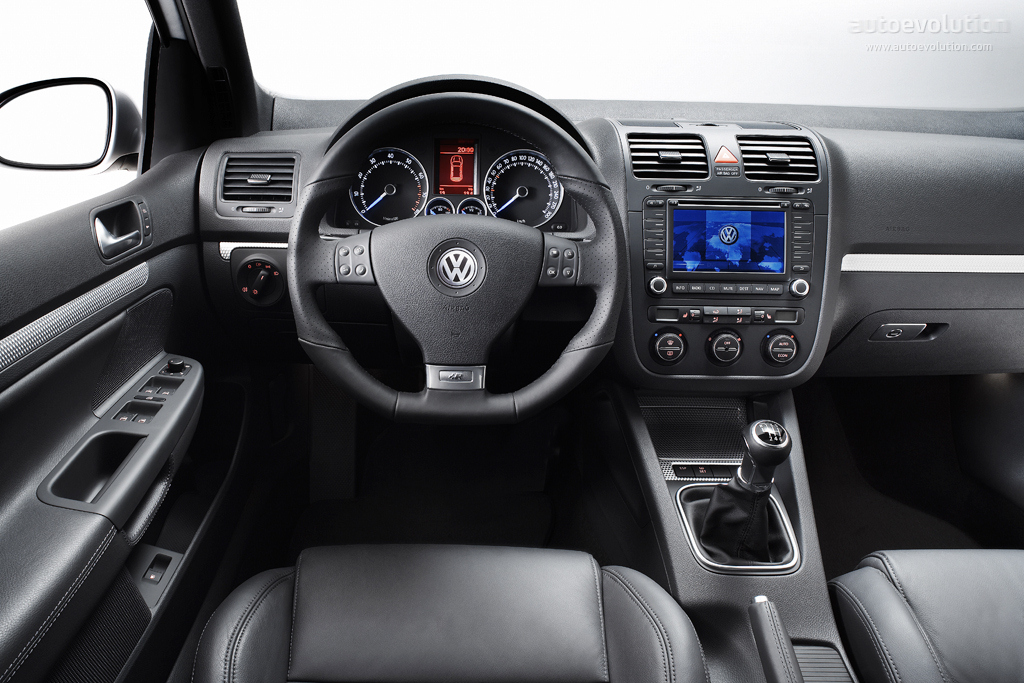
You need to lower 50 pounds of gear/mainshaft /tail housing assembly into the case. Before you start, be sure the tailshaft gasket is in place. (I put a little glue on it to keep it in position.) Now slowly lower the tailshaft/ mainshaft assy in, snake around the reverse idler and countershaft gears. I shoot to rest the mainshaft 'nose' on the edge of the input shaft 'cup' as a 'first stop' to give my arms a rest and to check my 'indexing'. If the collar slips-off, pull the assy back out and reset the collar & toggles.
Position the synchro and collar so your paint marks are lined up. Move the assembly in to stick the mainshaft nose into the needle bearings, as your assistant makes sure all the other gear cogs 'mesh' with the countershaft teeth. (Rotate the cogs on the mainshaft, don't turn the input / countershaft because that throws off your paint mark alignment.)
If you get all this stuff lined-up correctly, the whole assy just 'plops-together', without much fan-fair and you are done.
DD
Other parts and assembly tips
Heavy duty ball bearings are available, these will have more roller balls in them. (the more balls the better)
Some brands of brass synchro rings (stop rings) have oil relief grooves cast into them. These help channel the oil out of the friction surface for a faster grip and shifts, especially when the oil is thick and / or cold. (grooves can also be added but stay away from notches or thin sections in the stop ring, they can crack along any thin spot or added groove.
Always check the front ball bearing snap ring thickness to be sure it fits into the shallow counter bore in the front Input Bearing Retainer (IBR). Some snap rings are too thick and / or wide and will not allow the IBR to seat and seal on the gasket.
Inspect and deburr (file smooth) the teeth of the slider clutch hubs. (the hub where the 'toggle struts' mount)
On early 'flange type' 833, the 1st / 2nd shift fork is a 'stubby' brass piece. Replace it with the later 'wrap-around' fork for better shifting. Wrap around forks with the extra length thin extension on the end will need this extra length cut off.
4 Speed Manual Transmission 68 Vette 327 Engine
On later side covers with the stamped steel internal levers, it can be a challenge to install the 1st / 2nd 'wrap around' shift fork. On way to do this is to place the 3rd / 4th fork into the cover and then loop a flexible wire around the rear section of the levers, to allow the cover to drop onto the second lever. Once the cover is on the lever, the wire can be pulled-out. Another option is to leave the back-up light switch out and stick a thin probe through that hole to help align the fork to the cover lever detents.
Pay special attention to the front of the cluster gear counter shaft where it extends through the case. Seal this area carefully because it is a source of leaks. The side cover levers and the reverse light switch are other leak points to reseal. (new 'O' rings and reverse switch or case plug)
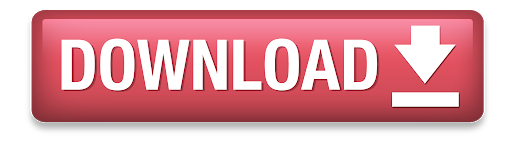
Comments are closed.